Hip Resurfacing Today
Bringing Everything Together
"The human mind accepts a new idea about as graciously as the human body accepts a foreign protein."
- Attributed to Wilfred Trotter, Consultant Surgeon, University College Hospital, London
Hip Resurfacing Can Work
It seemed to us that all the theoretical advantages of the hip resurfacing concept could be realized when thin metal shells were used as the articulating parts. However, this would require precision engineering for manufacture of the metal-on-metal bearing, with expertise virtually lost following the abandonment of metal on metal total hip replacements in the 1970's and a quality fixation that would be durable in young active patients.
Birmingham Experience of Metal-on-Metal Hip Resurfacing
Design of the hip resurfacing started in 1989 and the first implantation was performed in February of 1991. Over the next three years. three methods of fixation were employed on both the acetabular and femoral sides to determine optimum fixation. It was clear at the end of this pilot study that hydroxyapatite cups were best and cemented femoral components were best.42
Hybrid Fixed Resurfacing Components
A limited range of three acetabular components with hydroxyapatite coating on a largely smooth surface and three femoral components designed for fixation with cement were manufactured and inserted from March 1994. The early results with this implant were most satisfactory but, because of the limited range we could not treat very small or very large patients, nor could we deal effectively with significant acetabular dysplasia, and dysplasia is a common problem in these young patients.
Towards the end of 1996 a small number of patients with recently inserted Hybrid resurfacings reported a grating noise. This new complication could not be explained either by the Surgeons or the manufacturer, and there was no alternative but to withdraw this implant from the market place pending further investigation.
Subsequent investigation showed that the introducer holes for the cup introducer instrument had inadvertently been malpositioned. This meant that with introduction of the component at surgery, burrs could be raised on the articular surface giving rise to noise. Happily. the noise from these patient's hips settled quickly and all patients have continued to function well.
It was clear however that redesign of the implant system would be necessary so that a new cup introducer instrument could be employed, ensuring that there was no risk of damaging the articular surface with cup insertion.
Since re-design of the implant was required because of the introducer problem, the opportunity was taken to markedly expand the range of sizes available (4 cups increased to 23 cups) so that the extremes of patient sizes could be dealt with effectively. A dysplasia system was developed so that patients with severe acetabular dysplasia could be treated, and we decided to enhance the socket fixation.
It should be emphasized, however, that we have not encountered any problem with socket fixation in the original Hybrid components except in severe dysplasia, but contemporary work indicated that hydroxyapatite on a smooth surface might not prove durable in the long term as hydroxyapatite does get resorbed.26 Hydroxyapatite on a porous surface has the advantage of encouraging early bone ingrowth. When the hydroxyapatite disappears, then enduring biological fixation continues with bone ingrowth in the porous network.
It was clearly important to maintain continuity and commonality as far as possible in all other aspects of this project. To this end, the design team remained the same, Finsbury Ltd, the casting house, Centaur Precision, remained the same, the hydroxyapatite supplier, Plasma Biotal Ltd, remained the same as did the clinical development team, D.J.W. McMinn, FRCS and R.B.C.Treacy, FRCS. Only the finishing technologies changed significantly, to those developed by Finsbury Ltd, which were not available elsewhere but which allowed us much better dimensional control of the bearing surface geometry.
Development of Porous Ingrowth Surface - Porcast™
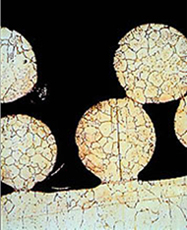
cup showing weak bead junctions.
It is known from clinical practice that conventional methods of producing a porous surface (plasma spray titanium and sintered beads) have a weak, mechanical link to the substrate material and the coating not infrequently displaces.
Particles can become lodged in the articulating parts and act as a third body. It was considered that this would be particularly detrimental to a metal on metal articulation, so a much more robust porous coating had to be developed.
In addition, we wanted to faithfully reproduce the metallurgical microstructure and chemistry of the McKee and Ring metal on metal hip arthroplasties which had given such good bearing durability.
-
1 year retrieval of polyethylene liner
showing embedded plasma spray
titanium particles displaced from
uncemented cup shell. -
Ring bearing microstructure
showing rich carbide content x 100 -
Carbide depletion
following HIP + SHT x l00 -
BHR components during casting process.
Ceramic coating of wax forms. -
Section through BHR cup showing
Porocast™ x50.
ingrowth surface.
It was discovered that the heat of sintering required to apply conventional sintered beads had a deleterious effect on the metallurgical microstructure and caused carbide depletion. Since carbides are the extremely hard ceramic-like particles in this high carbon chrome cobalt material responsible for wear resistance, any diminution of the carbide content could not be considered benign.
Furthermore, we noted that the processes of Hot Isostatic Pressing (HIP) and Solution Heat Treatment (SHT) commonly employed in manufacturing technology to eliminate microporosity and improve strength also had a deleterious effect on the microstructure by causing profound carbide depletion.
It has been shown that such carbide depleted metal performs poorly as a metal/metal articulating surface. 43,44,45,46
-
-
Birmingham Hip Resurfacing
showing porous
Beads are integral with substrate metal,
rich carbide content.
Porocast™ is a cast-in porous surface and the beads are integral with the substrate metal. This was a joint development between Centaur Precision Castings (a division of Doncaster Industries Plc), and Midland Medical TechnologiesLtd. In addition to the very considerable work that had to be undertaken in the development of the porocast process, the developers also had to satisfy the requirement that all the implants were porosity free. This then obviated the requirement for Solution Heat Treatment and Hot Isostatic Pressing as a post-cast heat treatment which, of course, would carbide deplete the metallurgical structure.
Finishing Technologies
It was clear that some of the early McKee/Farrar failures were due to poor manufacturing. In the modern era of metal on metal joints the highest possible technology is employed to achieve near perfect bearings. In the case of the Birmingham Hip Resurfacing, roundness to within two microns is achieved, an order of magnitude improvement on the conventional THR. Surface roughness is well within the ISO standard for conventional THR.
© 2007 Smith & Nephew